The passenger experience industry often considers plastics in aesthetic terms, from developing exciting new shapes, patterns and technologies to avoiding the ‘wall of beige’ in aircraft cabins, and everything in between. But as more and more of the plastics in other areas of our lives see developments around reducing their environmental footprint via using recycled plastics and bioplastics, what are the prospects for the cabin?
The answer is complicated. For a start, these aren’t single-use plastics, and despite their presence right in front of passengers’ noses, they’re not enormous by volume.
“While we do use some thermoplastics in our products for the aircraft cabin, the actual real estate taken up by thermoplastics is quite small,” Collins Aerospace spokesperson Joel Girdner explains to Runway Girl Network. “When we do use them, they are meant to last 20+ years and can be serviced. So they’re not considered the Fast Moving Consumer Goods (FMCG) most people associate with plastics and the immediate impact those have on say, landfill scenarios.”
“Plastics are lightweight materials,” emphasises Recaro CEO Mark Hiller. “This certainly saves our customers an immense amount of kerosene and CO2. This is a significant benefit if you consider the distances traveled by a seat of its lifetime. Many plastic parts are also re-used during refurbishment and are handed to the second or third customer.”
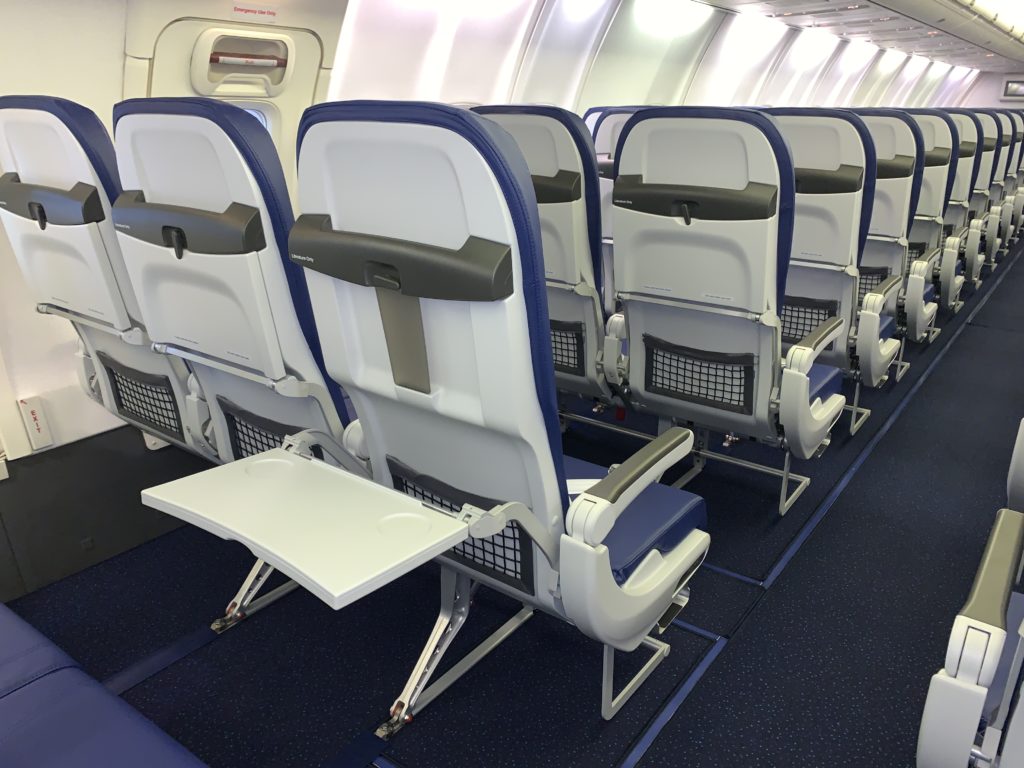
Seats are perhaps the opposite of single-use, but plastics sourcing is nonetheless important. Image: Recaro
Twenty-plus years of use is certainly admirable, but that sort of longevity also comes with harder requirements for materials standards: if it’s designed to last, the material needs to be structurally up to snuff.
“Almost every material or component we put on the interior of the aircraft has to meet some kind of flammability requirements, whether it’s vertical burn, smoke and tox, or OSU heat release,” says David McConnell, associate director for advanced materials and processes for interiors at Collins Aerospace.
That creates problems both for using recycled feedstock and bioplastics.
On the recycled feedstock side, says SEKISUI Kydex president and COO Ronn Cort, “currently there are no recycled thermoplastics in interiors on board an aircraft. A key blocker to using recycled thermoplastics is within the interior component manufacturer’s requirements, where the use of recycled plastics is not allowed. In addition, there are hurdles in recyclable material control, including identification and segregation of scrap.”
Kydex is, Cort says, working actively on the problem with the Aircraft Interior Recycling Association. So too is Kydex’s competitor SIMONA Boltaron.
In terms of the prospects of using sustainably created bioplastics rather than petrochemical ones, the need to ensure certification adds complexity, particularly around repeatability and consistency. If the properties of a bioplastic changes substantially, McConnell explains, it will need to be recertified — and that’s costly both in monetary and footprint terms. Moreover, supply of bioplastics is seasonal and dependent on production. All this adds uncertainty to the situation at present.
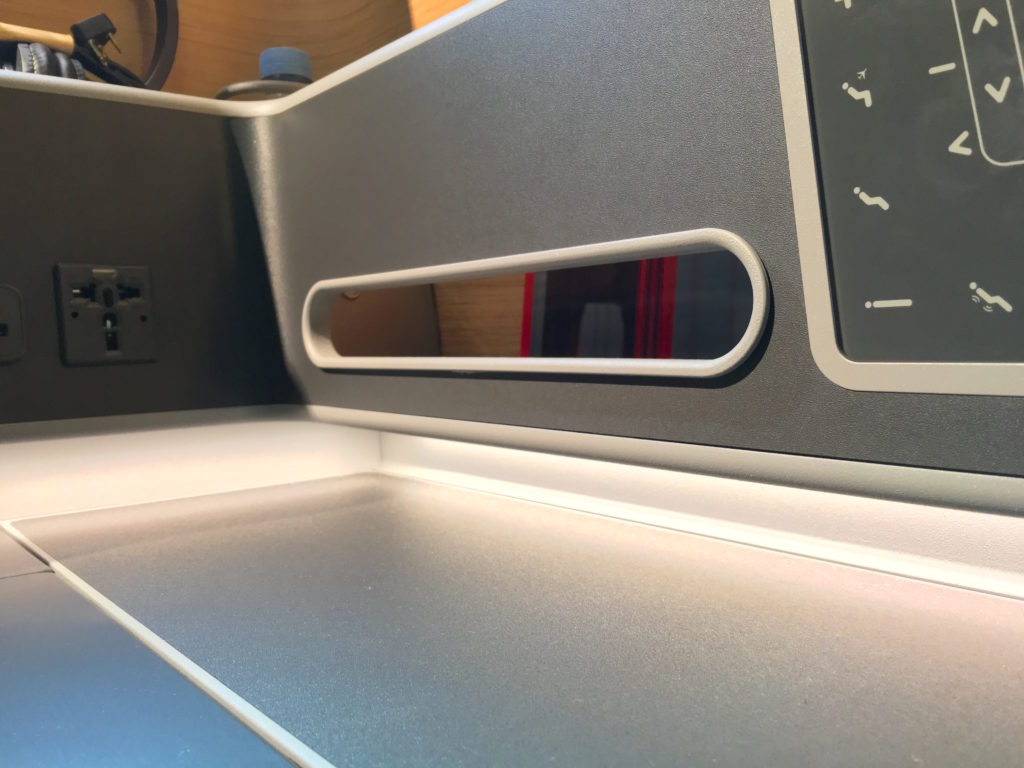
Onboard plastics in the seating area are highly engineered components with specific performance requirements. Image: John Walton
Indeed, says Mark Hiller, “in the past, there was already a research project on renewable plastics. Unfortunately, the material could not convince [us] regarding the processing procedure, so that Recaro didn’t consider the material for new seat projects.”
Research is, however, ongoing. Amélia Dedic-Roques, Safran Seats communications director, tells RGN that the interiors part of the French conglomerate is to launch an R&D project revisiting the recycled thermoplastics question.
Citing a need for “advanced technology that could be at least ten years away” to resolve the certification requirement issues, Kydex research and innovation manager Sean Stabler notes that, “since bio-based polymers are an organic material, most are more prone to burning and smoking compared to PVC/PMMA, PC, PEEK, PEK, PEI, PPSU and other engineered thermoplastics with additives which reduce flame, smoke and toxicity.”
Other bioplastics, meanwhile, are heavier at present than petrochemical plastics, leading to the prospect of greenwash and a false economy in the aircraft environment given the fuel footprint.
It’s clear there’s no silver bullet yet to reduce the opening of the thermoplastics footprint loop — but it’s equally clear that it’s one on the radars of a wide variety of interiors players searching for the technological breakthroughs to do so.
Related Articles:
- Slim seats are an eco-start but recycling makes bigger difference: AIRA
- Will rigid foams gain greater presence in cabin interiors?
- Super Eco Seat brings minimalism to new heights
- New year, new sustainable goals in commercial aviation
- Recycling solution for aircraft interiors moves closer
- Recycling aircraft interiors is achievable
- Flam testing? Know the law
Featured image credited to SEKISUI Kydex