In a development that could have significant benefits for aviation, a US laboratory is now printing high-temperature, high-strength 3D ceramic parts. Californian company HRL Laboratories utilises a resin that is 3D printed in the size and shape required, and then fired in order to convert it into a ceramic that can withstand temperatures up to 1700 degrees Celsius while retaining crucial strength.
“Our team surmounted the challenges inherent in ceramics to develop an innovative material that has myriad applications in a variety of industries,” HRL Sensors and Materials Laboratory senior scientist Dr. Tobias Schaedler explains. “The resulting material can withstand ultrahigh temperatures in excess of 1700°C and exhibits strength ten times higher than similar materials.”
“Ceramics are much more difficult to process than polymers or metals because they cannot be cast or machined easily,” says Schaedler, explaining that previously ceramics were created by sintering (compacting and forming a substance into a solid without reaching its melting point). That process limits the shapes that can be achieved, introduces pores to the final product and affects its strength. The sintering process creates brittle final products that do not hold up well to machining.
3D printing, meanwhile, deposits layers of the printing material, which was previously not resistant enough for high-temperature and high-strength applications. The new resin — technically a preceramic monomer — is laid down using stereolithography, a relatively standard and widely used 3D printing technology that focuses a UV laser on a vat of resin.
“With our new 3D printing process, we can take full advantage of the many desirable properties of this silicon oxycarbide ceramic, including high hardness, strength and temperature capability, as well as resistance to abrasion and corrosion,” notes Schaedler, crediting senior chemical engineer Zak Eckel and senior chemist Dr. Chaoyin Zhou with the formulation of the new resin.
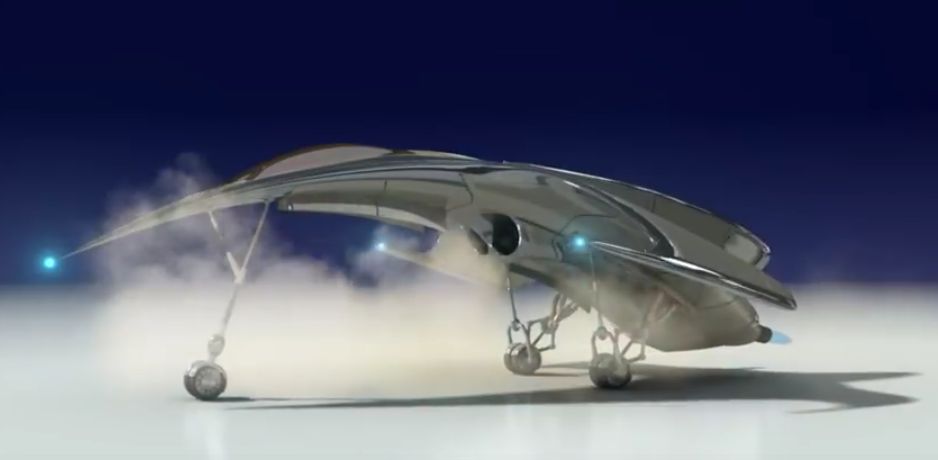
Components in jet engines and hypersonic vehicles, microelectromechanical systems and electronic device packaging are among the applications.
“This is an amazing breakthrough,” Eckel says in a video produced by HRL, explaining that the new ceramic resin and process “allows us to produce free-form ceramic parts of extremely strong and temperature resistant ceramics without out any machining, casting or compaction.”
“Everything from large components in jet engines and hypersonic vehicles to intricate parts in microelectromechanical systems and electronic device packaging could be fabricated,” Schaedler notes.
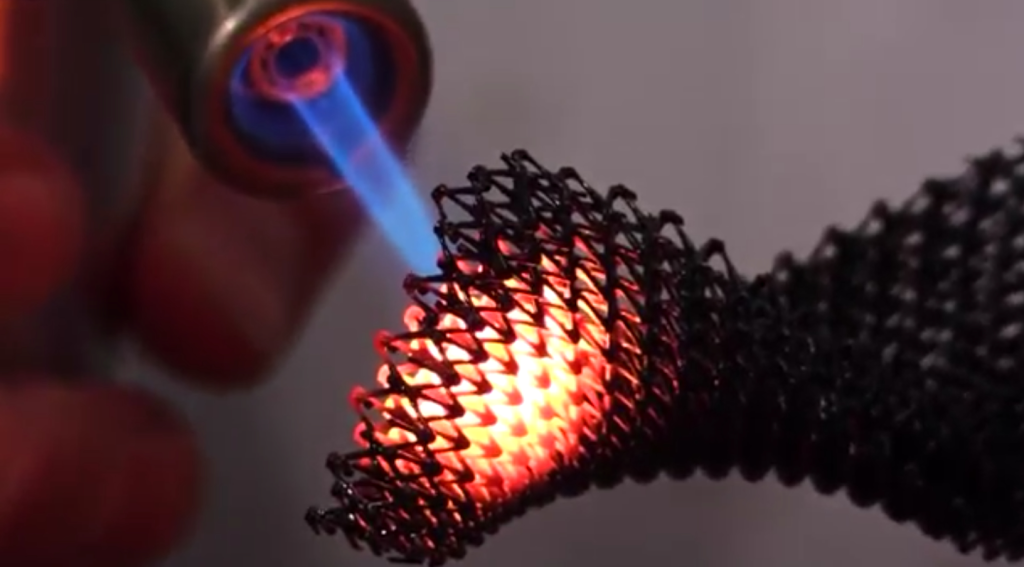
Exceeds 1000’C and does not melt or deteriorate
Further technical information about the research, which was funded by HRL and DARPA, is contained within a report in this month’s Science, Vol. 351 no. 6268 pp. 58-62. The abstract reads:
“The extremely high melting point of many ceramics adds challenges to additive manufacturing as compared with metals and polymers. Because ceramics cannot be cast or machined easily, three-dimensional (3D) printing enables a big leap in geometrical flexibility. We report preceramic monomers that are cured with ultraviolet light in a stereolithography 3D printer or through a patterned mask, forming 3D polymer structures that can have complex shape and cellular architecture. These polymer structures can be pyrolyzed to a ceramic with uniform shrinkage and virtually no porosity. Silicon oxycarbide microlattice and honeycomb cellular materials fabricated with this approach exhibit higher strength than ceramic foams of similar density. Additive manufacturing of such materials is of interest for propulsion components, thermal protection systems, porous burners, microelectromechanical systems, and electronic device packaging.”
HRL Laboratories explains the process of printing high-temperature, high-strength 3D ceramic parts in the following video.