In the context of unprecedented distrust in aviation safety regulation, largely but not entirely driven by the exposure of regulatory failures in the 737 MAX scandal, it is time for aviation, its suppliers, its regulators and the governments that direct their activities to review the industry’s current state and develop improvements.
It’s not sexy, exciting work: this is harmonisation of standards across separate sets of international regulation, distillation of details in disparate technical documentation down to their core principles to enshrine in legislation, or codification of the design requirements and certification specifications to provide confidence to all parties that the regulations are robust and incorporating recent developments.
And much of it — from almost shocking basics like accounting for angled seats or defining what a “serious injury” in airline seating context means, all the way down to specifying pass/fail criteria for head, lumbar, thorax, pelvis, leg and neck injuries, or using a range of simulated bodies that accurately reflects passenger reality — seems like it needs significant attention.
As part of a follow-up interview around Stelia’s new Opera 44° outward-facing herringbone for single-aisle, RGN discussed the state of play in regulation with the seatmaker’s head of programmes and support Sylvain Blanco and head of certification and airworthiness Benoit David.
Stelia is in a unique place as a EU-based company producing premium seating for both its parent company Airbus (regulated by EASA) and Boeing (regulated by the FAA) aircraft, in cabin configurations to be installed and operated by global MRO shops and airlines.
On the safety side, the system as it stands layers Special Conditions (SCs) and Certification Review Items (CRIs) that create equivalences to previous-generation seat regulations laid out in various parts of the US 14 CFR Part 25 or equivalent European regulations, particularly including 25.785, 25.561 or 25.562 in this case.
Discussing 25.785, David says “that paragraph is where all the nightmare starts for oblique seats and things like that” because that process says you need to ensure that a passenger will not have serious injury as a result of the 25.561 and 25.562 as a result of static and dynamic testing.
“And then that you have opened the Pandora’s box: anybody who is looking at dynamic test video can say: ‘I think that this could be a serious injury’.”
Indeed, ‘serious injury’ is not specified in the regulations: 25.785 (b) states only that “Each seat, berth, safety belt, harness, and adjacent part of the airplane at each station designated as occupiable during takeoff and landing must be designed so that a person making proper use of these facilities will not suffer serious injury in an emergency landing as a result of the inertia forces specified in §§ 25.561 and 25.562.”
It is hard to see how omitting critical definitions or pass/fail criteria is good regulation, and indeed the reactive strategy with Special Conditions and CRIs neither seems to be sensible from a holistic regulation point of view, nor is it particularly advantageous to industry.
Similarly, while the US Department of Transportation has regulations on equipping at least half of all aisle seats on aircraft with more than 30 seats with movable aisle armrests with the goal of enabling access by disabled passengers, this has not kept pace with the last decade and a half of seat design, particularly with regard to business class seat shrouding and doors. The crucial manoeuvre of transferring passengers from wheelchairs is still in many places a manual, poorly regulated, and often dangerously performed task. And there is no equivalent EU legislation for those companies certifying via EASA.
This regulatory lag and lack of harmonisation is an inherent challenge in all kinds of regulation, and industry innovations will, by their very nature, outpace the regulations developed to ensure the safety and access suitability of the previous generation of seats. But examples in other fields can surely be drawn upon here, because the alternative is inefficiency and, worse, safety flaws.
“From time to time during the development of a programme,” Blanco says, seatmakers will see “some changes in the interpretation of a regulation. That leads us to repeat some dynamic testing or to repeat some HIC testing, because of the new interpretation of the rules.” He points to a recent programme for a Boeing airframe last year as one example.
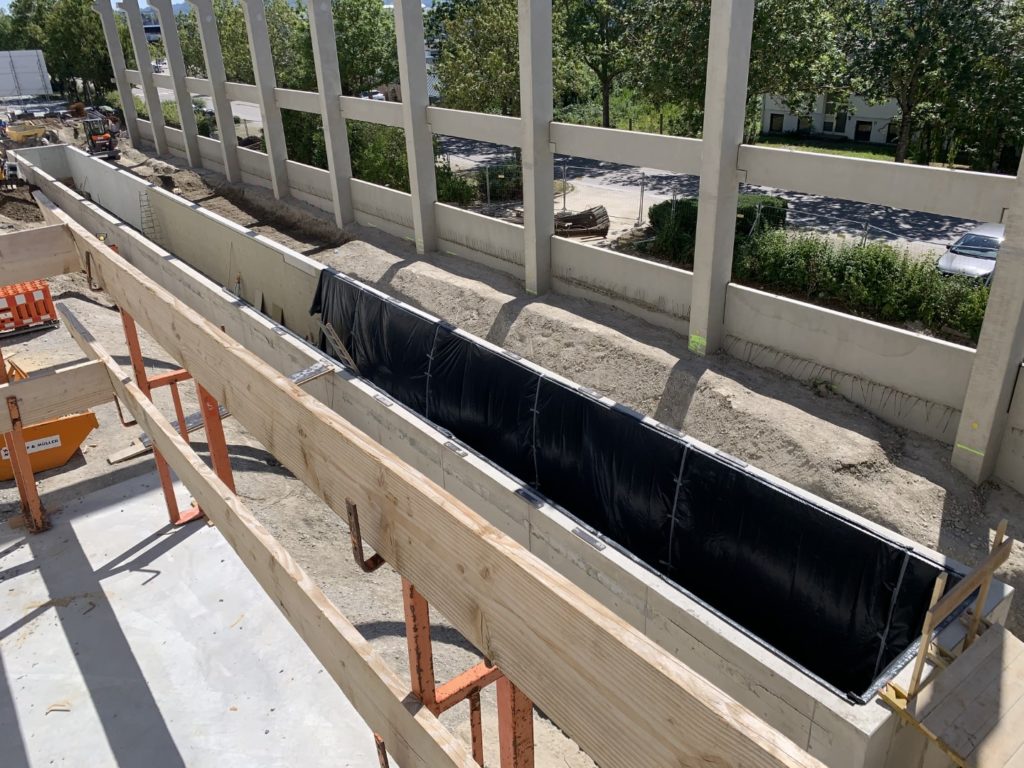
The complexity and cost of building testing equipment — like Recaro’s new dynamic sled assembly — are substantial. Image: John Walton
Does it make sense to retain this model in the future? Or should we start from, say, a principles-based or enabling regulation approach, acknowledging that there is an inherent and ongoing need for specific interpretation by regulators, and building a predictable and transparent regulatory system to reflect that?
Related Articles:
- Editorial: Test dummies should be updated to reflect modern traveler size
- Inside Stelia’s plans for certifying its Opera narrowbody seat
- Stelia sings 44°-angle tune with single-aisle Opera suite
- Airbus’ 4700nm A321XLR asks serious narrowbody PaxEx questions
- British Airways, Collins to revise Club Suite emergency door mechanism
- Regulations covering doored business class mini-suites evolve
- The prospects for business-plus as travel restarts
- Horizon scan: how PaxEx is changing during COVID and afterwards
- Recaro builds space to grow and new HQ flam, crash testing