SIMONA Boltaron, a thermoplastics specialist serving aerospace, mass transportation and other industries, is laser engraving its materials with special codes to ensure they’re fully traceable and can be properly repurposed when they reach their end-of-life including as aircraft interiors.
“We are working with AIRA,” the Aircraft Interior Recycling Association, SIMONA Boltaron technical director Samantha Stacy told Runway Girl Network at the Aircraft Interiors Expo in Hamburg.
“So, they did test all of our materials and give them codes and we are actually laser engraving our materials with those codes.”
The programme got underway over the last year, and now “anything that leaves our facilities is traceable,” confirmed Valerie Glover, the new marketing manager for SIMONA AMERICA Group, which boasts three independent manufacturing sites in North America including SIMONA Boltaron.
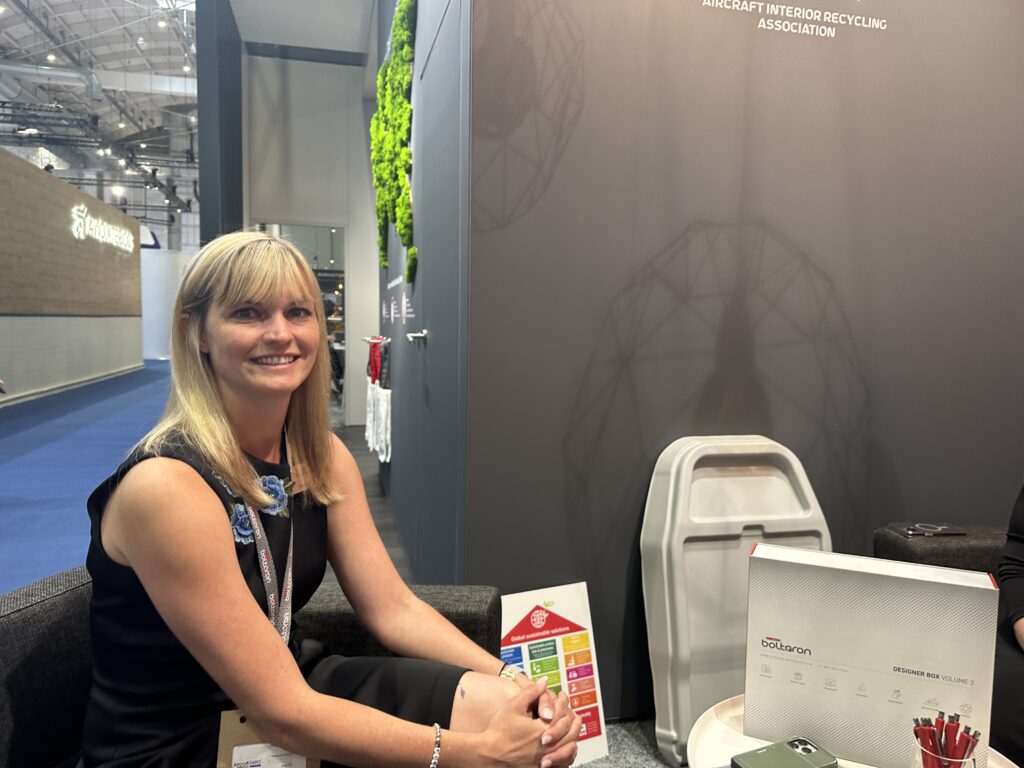
SIMONA Boltaron technical director Samantha Stacy explained the firm’s sustainability work at the Aircraft Interiors Expo in Hamburg.
Headquartered in Newcomerstown, Ohio, SIMONA Boltaron is understood to be the only plastic sheet manufacturer in aircraft interiors that can extrude, calendar and press laminate sheet. This means that 100% of its content is made at one site using similar chemical formulations, enabling the firm to recycle internally both film and sheet products.
Aerospace-grade thermoplastics are a bit unique. They are used in everything from economy class seatbacks and premium seat furniture to galley and lavatory components, but once used on aircraft, they can’t presently be recycled for reuse onboard due to stringent flammability requirements. By working with AIRA, SIMONA Boltaron is helping its customers find secondary non-aerospace recycling applications for its now-coded materials.
Outside of labeling its materials and facilitating the repurposing of aerospace-grade thermoplastics, SIMONA Boltaron offers its so-called 9865 and 4365 Terreform recycled-grade sheets for aviation clients. Terreform is made of recycled scrap from various Boltaron materials including aerospace-grade scrap (not from aircraft interiors that have already flown). The material might otherwise end up in landfill.
Offered in several baseline colours, the product can be molded into aircraft interior parts where aesthetic perfection is not a requirement. And whilst it cannot be used for the sort of decorative translucents breaking cover at top tier airlines, it can be mixed and matched to provide a customised palette for operators, noted Stacy.
“We want to make sure that, okay, we’ve created this recycled grade, but we’re not just doing it as a feel-good moment. We want to make sure that the carbon footprint is actually lower when you’re choosing this [Terreform 9865] product over a standard 9000 series,” she explained.
“So, this product we say is a minimum of 50% recycled content and that, according to our calculations, is about a 26% reduction in carbon footprint.”
Italian seatmaker Optimares has rather famously used Terreform on elements of its new SoFab business class seat, including the table, electrical box and wireless charger.
Stacy refers to Terreform as “our first step” towards a more sustainable product. “So, it’s not all the way to a fully circular product. Obviously, that’s the goal someday in the future.”
More broadly, however, SIMONA Boltaron sees an opportunity for the aviation industry to make a bigger sustainability push by streamlining seat design to aid in recycling efforts.
“It’s about looking at the end seats [and asking] ‘how can we design these things to be taken apart?’ Because there’s a lot of different materials that can’t be recycled together,” said Stacy.
“So, I think that that’s going to be a big change that the industry is going to have to look at. How do I design this so that I can take it apart at the end of life as well.”
Acro Aircraft Seating is among the aircraft seatmakers focused on that very remit. To wit, it has also worked in partnership with AIRA to create a full digital database of the parts in its popular Series 9 and Series 6 economy class seats.
“This database can be used by airlines to ensure the proper identification, separation and responsible recycling of materials used in seating components once they reach the end of their useable life,” Acro CEO Neil Cairns told RGN.
For AIRA director Tony Seville, there is no excuse for manufacturers to make aircraft seat parts that are not 100% recyclable.
Interestingly, SIMONA Boltaron’s Stacy also revealed that the thermoplastics specialist is exploring the use of bio-based materials “where it makes sense” as part of the three pillars of its sustainability work.
Another pillar is about ensuring its production processes are more efficient. “So that plays into the product carbon footprint as well,” she said, “how much energy it actually takes up.”
As a stock-listed company with headquarters in Kirn, Germany, parent company SIMONA AG adheres to European Union law, including the Corporate Sustainability Reporting Directive that requires firms to report on the impact of their corporate activities on the environment and society. Embracing sustainability at every rung of its business, the firm has appointed three full-time dedicated employees to focus on sustainability — two in Germany and one in the US.
Sustainability, stressed Stacy, is important to the whole company.
Related Articles:
- Acro CEO on why Series 9 recyclability is only the beginning
- Perfectly imperfect: Aviation explores beauty of recycled interiors
- Divine divan? Optimares SoFab persuades with comfortable simplicity
- How Scottish Leather Group delivers sustainable leather for airlines
- How SIMONA is embracing sustainability at every rung of its business
- ‘No excuse’ for making non-recyclable aircraft seats: AIRA
- Boltaron achieves true recycling of aerospace grade thermoplastic
All images credited to the author, Mary Kirby