TOULOUSE — As Japan Airlines’ (JAL) first Airbus A350-1000 waggled its wings on takeoff from Blagnac en route to Tokyo, the airline’s executives seemed very pleased with the much-delayed gift arriving under the tree at Haneda Airport this December. While the design, aesthetics and functionality of the seats are impressive, much of the discussion swirling in Toulouse was about the supply chain delays impacting aircraft interiors, and the knock-on effects to the airline’s product update plans and aircraft route rollout.
JAL is fortunate in that its 2023 financial year, which stretches to March 2024, means that its stated plans for delivery of three aircraft in 2023 are possible, enabling a daily roundtrip to New York and the start of services to Dallas-Fort Worth. But with three A350s in Toulouse on delivery day — one now in Tokyo, one having exited the final assembly line, and one in final assembly — the effects of delays in the aircraft’s cabin interiors were all too visible, and indeed all too prone to being replicated elsewhere in this strongly consolidated part of aviation’s supply chain.
Yamanaka Jun, JAL’s vice president for engineering and quality assurance Europe — essentially the airline’s main exec in Toulouse — told Runway Girl Network (a guest of Airbus at the event) that “the difficulty was a lack of certain parts, and also the requirements of additional time for assembling the seats in Toulouse compared to assembling these seats in their factory.”
The Safran Seats GB-manufactured seats for the aircraft’s first and business class cabins are manufactured in Cwmbran in South Wales, while the Safran Seats France premium economy products are manufactured in Issoudun in central France.
More widely, Yamanaka told RGN, “we had difficulties, it is true, because the materials or the parts are not really available due to the Covid pandemic, as well as the conflicts of the world… giving us difficulties obtaining the parts and the materials, and that is really giving the delays in the on-dock of the seats’ manufacturing.”
Onboard, the Safran products are in admirable shape — although the delays should have ironed out visible quality issues — but in the details a few issues are notable within the business class cabin.
The most obvious issue is a materials one: the polystone used as the side table is, while attractive, not particularly durable, with substantial scratching. On the aircraft, Yamanaka discussed openly with this journalist the complications of finding a replacement for the polystone elements: these are not easily swapped out. These issues are surprising, since polystone is relatively new but has been demonstrated as a core material to Safran’s Unity seat platform.
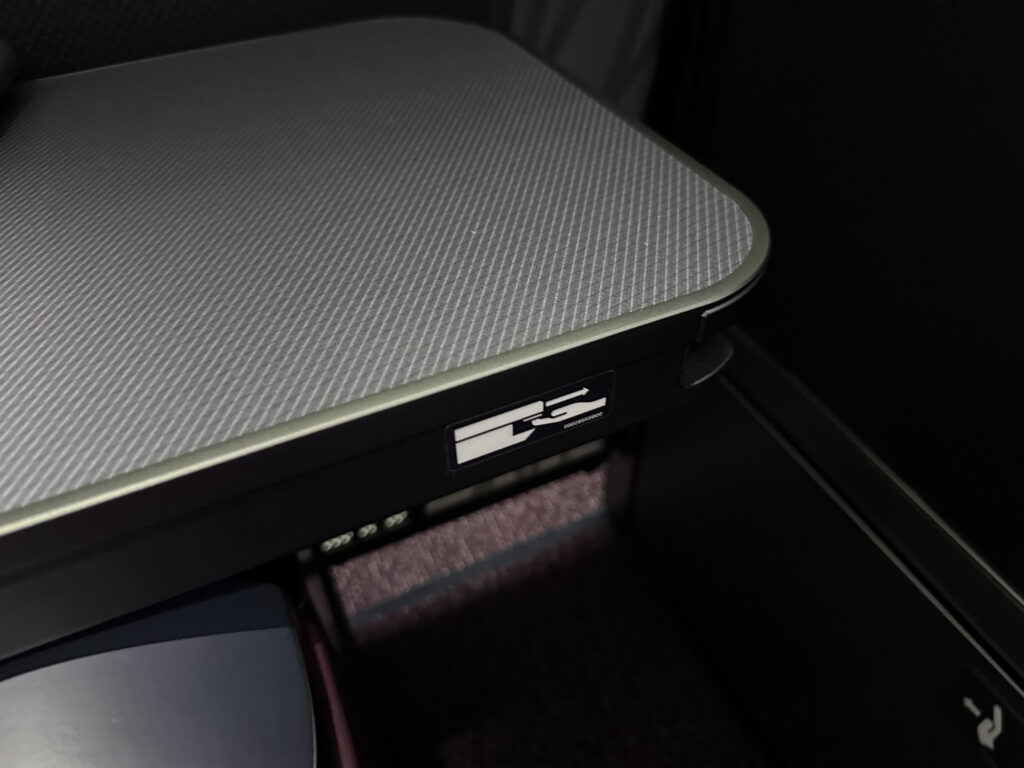
The table latching system seemed clunky, and it will be interesting to see how this works with passengers. Image – John Walton
Elsewhere, some seat element join issues were present, but substantially fewer materials quality problems than might have been feared were visible. This is likely due to the months of delays allowing quality and perceived quality issues to be resolved.
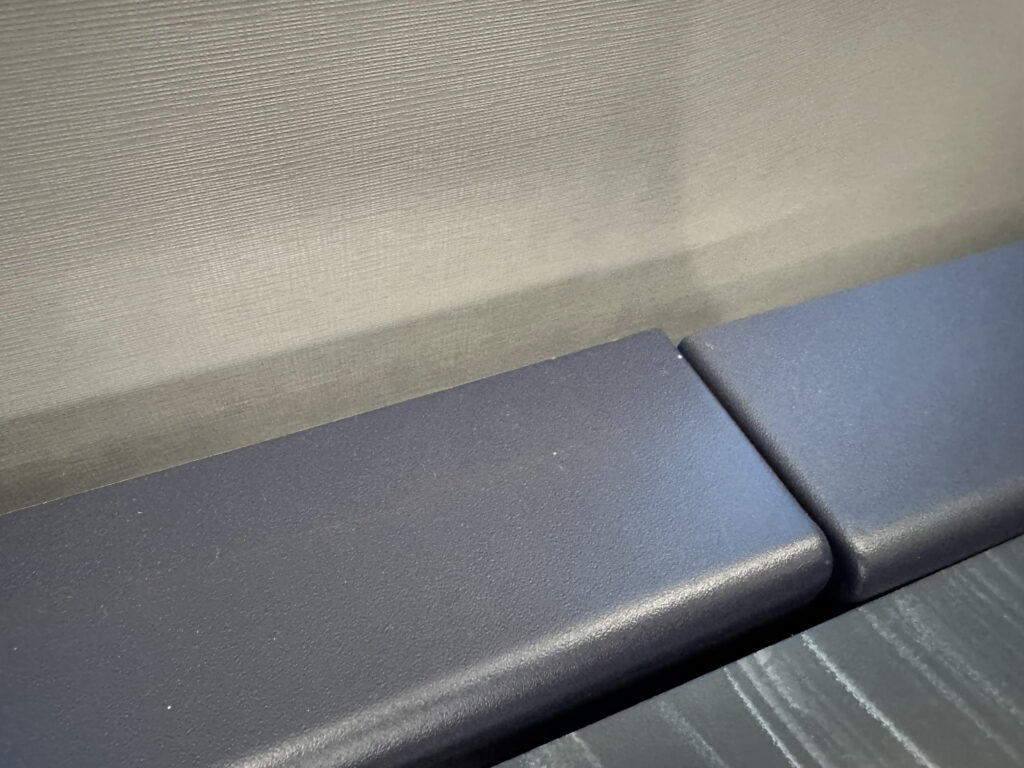
Some — but in fairness, not many — perceived quality issues were visible on board. Image: John Walton
JAL — and designers tangerine — have been smart in reducing the number of like-to-like material joins within the cabin. This is not only an aesthetic decision to reduce expanses of identical thermoplastics, but also means that matching patterns and materials is not required at all or offers more flexibility when it is needed
The airline seems content with the product as delivered, and Yamanaka noted that, “right now you can see the products: that is really super, very high quality seats, [that] now they achieved. But initially, due to the lack of the parts, it’s not complete when the first shipset of the seats arrived to the factory in Toulouse.
“But now you know, step by step, one by one, they get the parts they adjusted, they’ve manufactured everything perfectly, and finally, the products you have seen here is achieved. So I’m very satisfied with their achievement.”
Nishigaki Junta, project manager for product and service development, summed up the issue and its root causes in response to questions from Runway Girl Network as “a difficult question indeed, and my answer will only be on a hypothesis. But I think the major cause of the delay was the Covid-19.
“Of course there might have been several causes that were specific to Safran, but the major cause was the supply chain disruption during a global pandemic and so therefore the same similar delay might have happened with other suppliers.”
No supplier has been immune to production issues, and it will be notable to see how the remaining deliveries of JAL’s A350-1000s shape up following this head-of-version airframe.
Beyond the JAL examples, too, these Safran seats have also been selected by Qantas (first and business class) and Air India (business class) in the coming months and years. For a launch product, JAL’s version of Unity was relatively highly customised compared with the display models at the last two Aircraft Interiors Expos, with its wardrobe doors, side-swing table and shoulder-side stowage.
Given the delays to JAL’s aircraft, it will be instructive to see how the programmes for these — and any other — airlines’ aircraft proceed.
Airbus provided flights and accommodation to the event, but as ever all opinions are of the author.
Related Articles:
- JAL’s new flagship A350-1000 astounds with aesthetics and space
- JAL first class continues to shine despite delayed hard product
- Japan Airlines reveals stunning A350-1000 interiors but delays launch
- Recaro sees demand, supply chain and diversification opportunities
- Safran’s Unity adds premium stagger to its business lineup
- A spiky 2023 for business class supply chain, production and demand
Featured image credited to John Walton