HAMBURG — Supply chain constraints and labor challenges in aviation continue to create headaches for OEMs, their suppliers and airline customers. In a bid to tackle the issues and meet its deliverables to airframers, Laupheim, Germany-headquartered Diehl Aviation is pulling several key levers including building stock buffers and providing advances to cash-strapped suppliers, company CEO Dr. Jörg Schuler revealed to RGN at this year’s Aircraft Interiors Expo (AIX) in Hamburg.
Buffer stocks, double sourcing, cash
“The supply chain disruptions are still there,” said Dr. Schuler when asked if the post-shutdown bottlenecks highlighted by Diehl Aviation and other interiors giants at last year’s AIX had eased.
“It’s still the same struggle to manage the supply chain and we’re putting a lot of effort into managing our Tier 1s and even Tier 2s or Tier 3s. So, we are not focusing only on the first ones in order to fulfill our obligations towards the OEMs.”
He continued:
We are building inventory buffer stocks. We try to double-source. We support suppliers with cash in advance. But there is still a lot of effort to stabilize the supply chain and they are suffering still from the Covid times. They had credits; now they have high interest rates to pay them back.
Our suppliers still have difficulties always to get people on board. So also, it’s not only digesting Covid in the past. Now it’s a matter of how to ramp up. The whole industry is ramping up and they are running up and we are really trying in an everyday fight to support our supply chain, to keep it robust, to follow the OEMs’ rates. So that’s our obligation, our duty. And there’s a lot of effort behind the supply chain.
Labor issues, and addressing traveled work with rework
For Diehl Aviation, labor capacity is not an issue, he said, but: “we lost through Covid a lot of critical skills and competencies and we now need to renew. In terms of pure capacity, we are okay now.” Labor does remain a challenge with some of the smaller suppliers, however. “There are still a few small ones who suffer getting the right people,” he noted.
Missing parts are “a consequence of the weak supply chain”, the Diehl Aviation CEO also confided. So, some content is arriving not fully completed. “This is where our biggest fight is also in our production; we often touch a product two or three times because then we install the missing parts later, so rework is fairly high. So, you have not a very lean production flow because of the disruptions coming from the supply chain.”
Diehl Aviation has long had a presence in the United States, including in Everett, Washington and Sterrett, Alabama. And more recently, it established on-site support for Boeing’s final assembly line in Charleston, South Carolina, and bolstered its Everett-area presence with a new collaborative space. During AIX, it announced the establishment of a new Mexican subsidiary, a production plant and office space which will employ roughly 500 staffers in the medium-term, and start production — initially of the A220’s new spacious overhead bins — in 2025. The A220 is being assembled in Mirabel, Québec, Canada, and Mobile, Alabama.
The drivers behind securing this new location in Mexico, said Dr. Schuler, are threefold: “It’s very much helping us in terms of customer centricity because being in Mexico, you can nicely serve in the Americas, Embraer, Airbus, Boeing and Bombardier. So, you have all the big OEMs on the continent.”
“We have a nice access to talent as well,” he continued, “because we are not only doing production but also engineering developments we want to do there. And last but not least you have still a cost competitiveness. So, we want to build up also a local supply chain to serve this plant. So, these are the key drivers. But first of all, it’s customer proximity.”
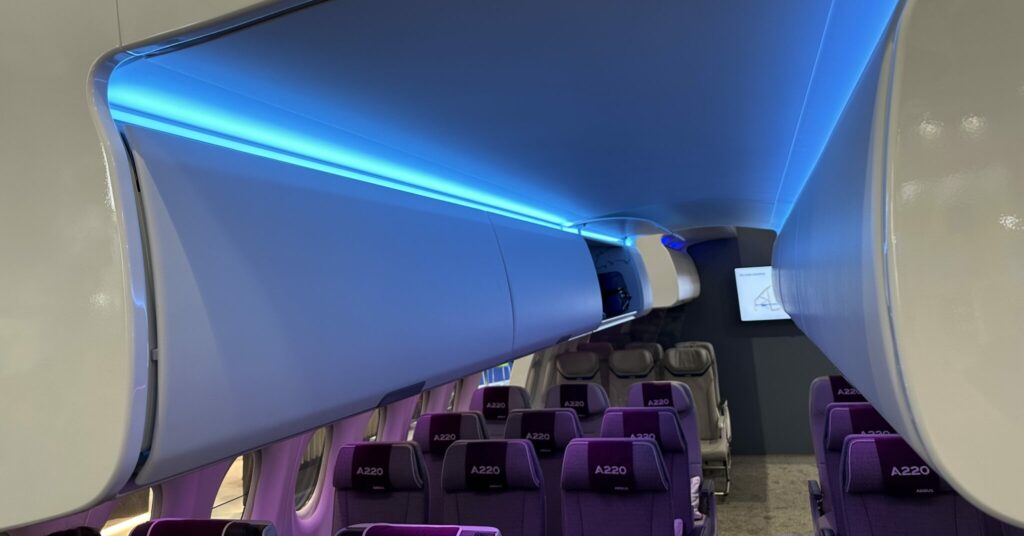
Diehl Aviation’s new plant in Mexico will build the Airbus A220’s new spacious overhead bins, which were first revealed at last year’s AIX in Hamburg. Image: John Walton
Closer proximity to the big airframers also works from a time zone perspective.
Diehl Aviation’s new Customer Collaboration Space at its Everett logistics support site near Seattle, meanwhile, is going “very well”, said Dr. Schuler.
“[W]e have a lot of exchanges with the Boeing teams, but it’s also intended to be for North American airlines and to visit us there. So, we can basically do what we do here [at AIX], demonstrate our competences, our products, our philosophy and you have people on site, face to face meetings, speaking and exchanging what we can do, and how we do it. It’s a better place for collaboration.”
Sustainability initiatives
Those meetings increasingly address industry sustainability. Diehl Aviation sees itself as the “frontrunner” in solving big trends in the cabin, including around sustainability and connected cabin management.
Its so-called ECO Thermoplastic Ducting is now flying as standard on Airbus aircraft, and its lightweight ECO Powder Coating, which replaces decor foils in the cabin, is ready for prime time.
Indeed, Diehl Aviation has made a big investment in powder coating machines and will be able to provide it for single-aisle aircraft “as soon as Airbus is willing to do it” but can also do it on long-range aircraft, said Dr. Schuler.
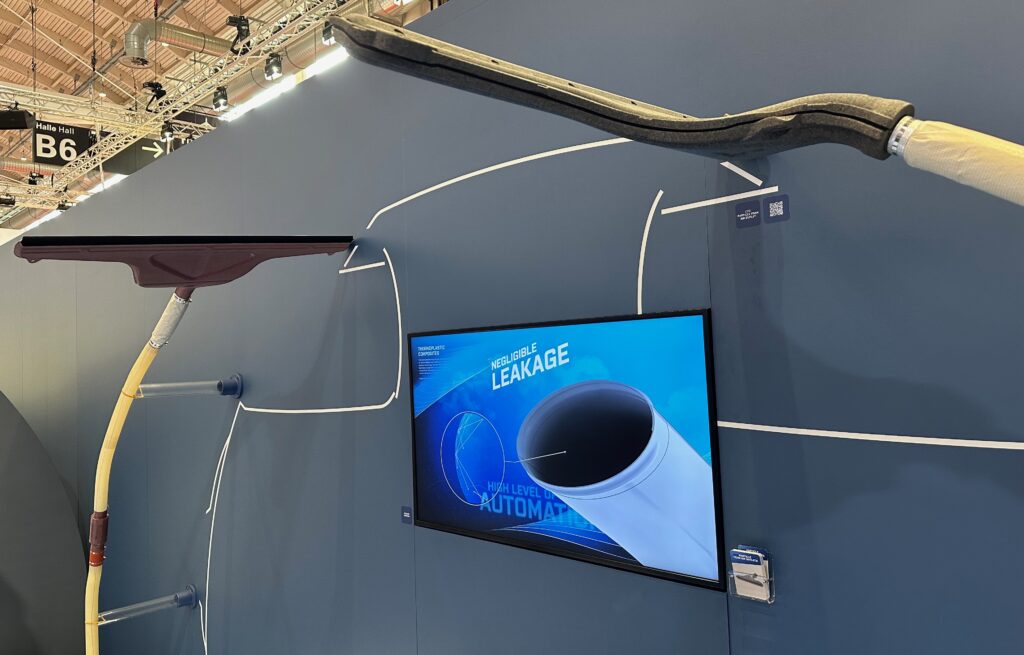
ECO Thermoplastic Ducting, which boasts new efficiencies and weight reduction, was on display at the Diehl Aviation stand at AIX 2024.
Diehl Aviation’s new bio-based ECO Sidewall is an eco-efficient sidewall concept that sets new standards in sustainable aviation through the use of lightweight materials including basaltic prepregs and a Kevlar® honeycomb core. The innovative design, which won the 2024 Crystal Cabin Award for Sustainable Cabin in Hamburg, could be flying soon.
Developed in partnership with 9T Labs, Diehl Aviation’s ECO Bracket, meanwhile, slashes weight and production costs by 50%, and was shortlisted for a Crystal Cabin Award, “It’s only a matter of the customer qualifying it. I mean we have everything. We can produce it. So it’s a matter of qualifying it through the customer,” said Dr. Schuler of the ECO Bracket. Hundreds of brackets are needed per jet.
More broadly on the eco-aviation front, Diehl Aviation is a key partner on several eVTOL projects.
The company believes it is also well positioned to address the most positive trend to emerge from AIX, cabin accessibility, as Diehl Aviation showcased its Skypax wheelchair-accessible galley/lav module back in 2022. “I would say we have all the competences, all the knowledge to make this happen,” said Dr. Schuler.
He reckons that Europe will be the next to pursue aircraft lavatory accessibility rulemaking, after the US paved the way in 2023 when it announced a final rule to bring truly accessible lavs to new narrowbodies in the next decade.
Related Articles:
- Inside Airbus’ Airspace 2025 bin changes, including retrofits
- JAL A350 interiors supply chain issues raise spectre of delays in 2024
- Recaro Aircraft Seating CEO flags continued shortage in IFE parts
- Several eVTOL projects and their suppliers hit key milestones
- Diehl opens collaborative space near Seattle, eyes wider US footprint
- US DOT’s expanded lav rule for narrowbodies still a decade away
- How Diehl and HAECO have reimagined the single-aisle premium cabin
- Diehl demos Skypax wheelchair-accessible galley/lav module