Airlines and passenger experience industry suppliers are attempting to reassure passengers and staff that aircraft cabins are as safe as possible during the COVID-19 crisis in a variety of ways, from mask policies to individually branded cleaning programs, from barrier shielding to changed inflight service, from physical distancing to the use of long-lasting cleaning products.
Lufthansa Technik is currently in the process of testing TiTANO, a biocide from German company HECOSOL, for use in the airline cabin as a long-lasting virucide, effective against coronavirus’ like SARS-CoV-2, which causes COVID-19.
The maintenance, repair and overhaul provider tells Runway Girl Network that the product is used widely in public areas, including shopping centers, hospitals and the food industry, and that it is testing applications on cabin surfaces including overhead bins, tray tables, armrests and sidewalls via electrostatic spraying.
“Everything is driven by doing intensive cleaning after each flight,” head of product cabin modification Georg Stoffelen tells RGN, highlighting that Lufthansa Technik is aiming to ensure hygienic conditions remain even after the initial flush of deep-cleaning is relaxed.
“The virus protection, killing the virus, is valid for one year: one time you spray the surface, and it’s sealed for one year. Even if you clean with sharp cleaners, it will not go: it will stay on the surface, permanently killing viruses that come onto the surface,” Stoffelen explains.
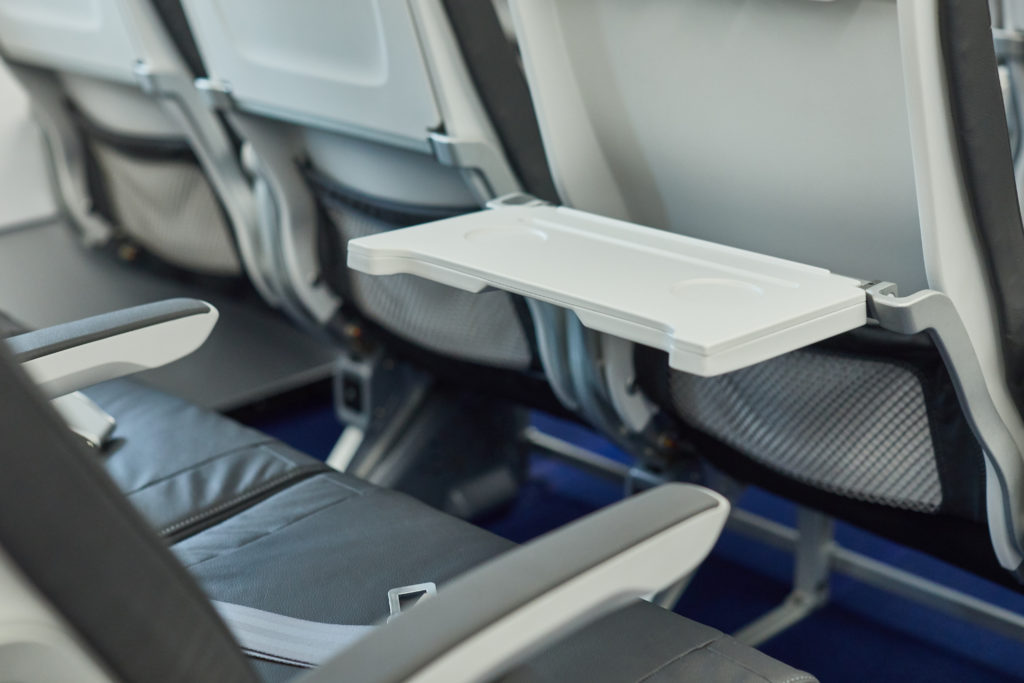
Virucides will be sprayed on all surfaces including high touch areas like tray tables. Image: Lufthansa
One issue within the cabin is that many virucidal disinfectants require UV light to work, Stoffelen highlights, and part of the intellectual property behind the TiTANO product is that it does not require light, and can thus be applied inside an aircraft cabin and at night.
There are many challenges, of course, around ensuring that any new product is both safe for humans in the confined spaces of the cabin.
Lufthansa Technik is expecting to issue an engineering bulletin within the next month or two to outline its processes.
“EASA is not requiring certification of this,” Stoffelen explains, “so we made our own, because we want to make an engineering bulletin later on to secure that the work we’re doing is safe.”
“Because we do electrostatic certification of our liquid, we have to look at material testing, for aging, for wear, for corrosion and for discoloration,” Stoffelen says.
“We put samples of seven different materials — what we’re flying in our fleet [at] Lufthansa — and are checking this material [to see] if the liquid has any influence on the surfaces.”
Since TiTANO has been used since the mid-2010s in on-ground public spaces, there is some safety read-across, but Lufthansa Technik isn’t taking any chances and is conducting tests with real-world aircraft seats.
“Nearly all material tests are ongoing,” Stoffelen explains. “Last week we started. We have no major [problems]. We already sprayed our seats, because we have some spare seats, and nothing happened: no discoloration. We are quite confident that we have a good result.”
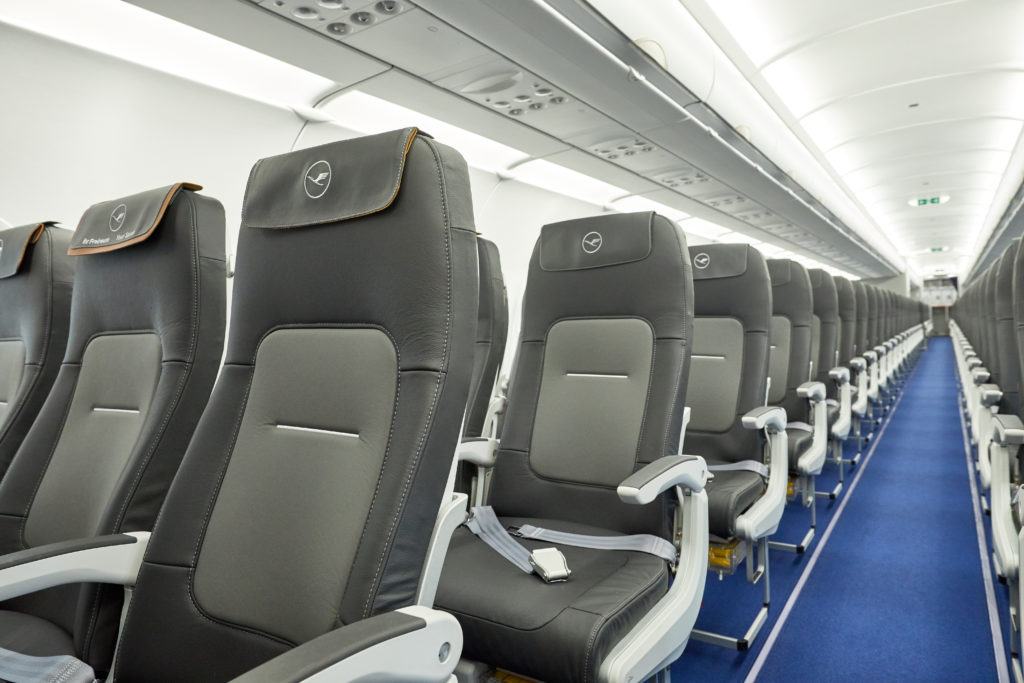
With leather commonly used as a seating material, discoloration and premature aging is a concern. Image: Lufthansa
LHT is also testing for public health safety, including toxicity and allergies, with its in-house laboratories that have carried out previous testing for “all cleaners that are used on aircraft, and all those things we test anyway,” Stoffelen says. “We put Titano through the same method [of] testing.”
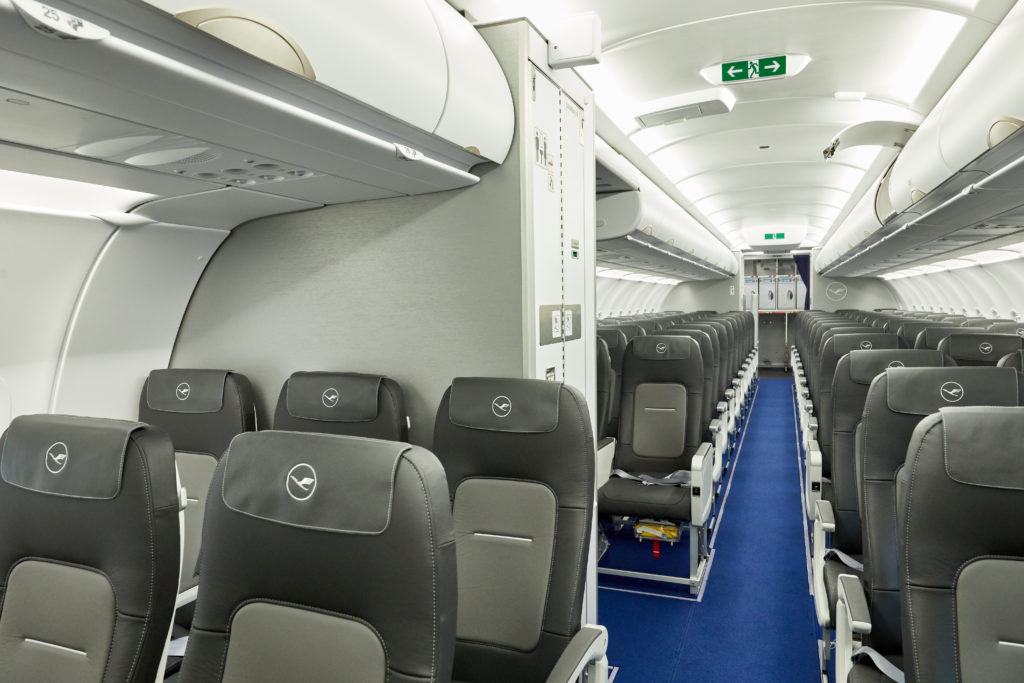
Any product used in the cabin must be effective and safe on a variety of surfaces from seats to walls to floors and more. Image: Lufthansa
Corrosion testing for metals is a time-consuming part of the program, since cabins and seats contain a variety of different types of metals and different alloys, and is the most complex part of the testing, Stoffelen notes.
With its own laboratories that are used to carrying out this kind of work, the company estimates that will be able to complete the certification process roughly two to three months more quickly — and to pivot more quickly within the testing — than if it had to outsource the work to third-party testers.
Related Articles:
- Honeywell pivots to providing tech to get people flying again
- Boeing seeks to build confidence in air travel through data
- Need for hygiene standards for cabin surfaces in the spotlight
- Airbus launches internal program to innovate for post-pandemic travel
- Flight experience as we know it will change: Collins Aerospace
- Crystal Cabin Concepts that address passenger health prove timely
- IFEC ready to aid airlines impart new inflight protocols to passengers
- Industry stakeholders weigh likelihood of major cabin reconfigurations
- Traveling with an allergic child trained me for a post-pandemic world
- Flying amid coronavirus outbreak: China suggests PaxEx changes
- Latitude Aero shifts focus to aircraft cleaning and decontamination
- Travel advice, aircraft disinsection and caution over Zika virus risks
- Press Release: New Boltaron product passes UV-C test by GermFalcon
- Press Release: Honeywell offers safety packs for passengers and crew