Soisa Aircraft Interiors, the Chihuahua, Mexico-based firm that specialises in aircraft seat dress covers, cushions and other services, attended this year’s Aircraft Interiors Expo in Hamburg with two key messages: its new buyer-furnished equipment (BFE) dress cover management programme can deliver immediate cost savings and reduced lead times for airlines; and its new organic armrest is poised to improve their eco-credentials.
Under the ‘BFE management’ programme, an airline directly procures its dress covers from Soisa as opposed to procuring them from a seatmaker which might then turn to Soisa to produce them.
Sharing color around the current paradigm, Jacobo Mesta, who now leads Soisa’s sales and growth strategy said: “Imagine the airline sending the purchase order to the OEM, the OEM telling us to manufacture it, us manufacturing it and sending it to the OEM, and then they send it to the airline, instead of the airline [going] to us directly.”
By flipping the script, and having seat cover specialist Soisa involved from the very beginning — assuming responsibility for on-time delivery — he said airlines can expect far better lead times and substantially reduced costs, whilst consistent part numbers throughout the aircraft’s lifecycle eliminate re-engineering and certification costs.
“There are deals that we can do with the OEM; there’s direct shipment authorisations, there’s royalties that we pay to the OEM. But as long as we can do it faster and directly, it’s going to help the airline huge,” he told Runway Girl Network.
This approach can also relieve the seatmakers of capital costs, administrative burdens and supply chain complexities, he said, as Soisa “is dealing with the materials, buying the materials, and getting it on time. So the responsibility comes to us now instead of the OEM and we have to deliver on time on their assembly line. So, they can just assemble the seats really fast, put the seat cover on it, and get it out.
“So that is a way of really reducing the lead time and [streamlining] the supply chain. Because we do see a lot of constraints.”
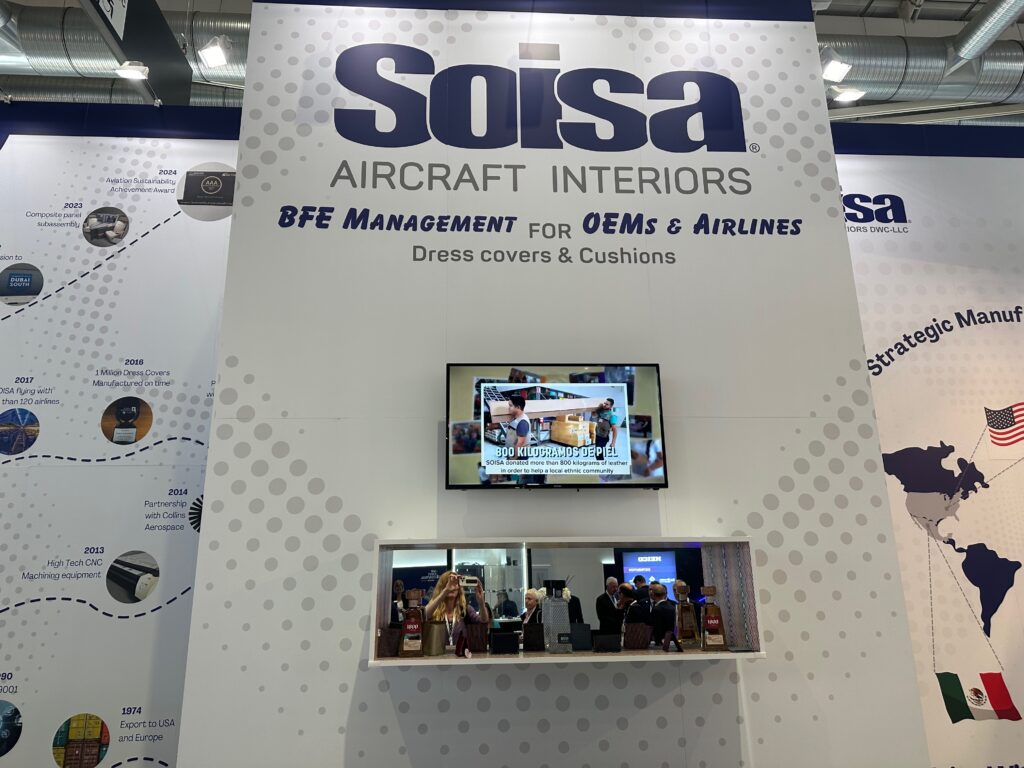
Soisa Aircraft Interiors highlighted its new BFE management programme at AIX 2024. Image: Mary Kirby
Reducing the number of manufacturing sites involved in the production of any given product also improves sustainability, as it reduces transit times and lowers carbon emissions.
“I think one of the best things we need to do right now is [address] how we can reduce the supply chain lead time, how we get as close as possible to our clients. Because you cannot be shipping leather or Velcro or everything from all over the world,” said Mesta, who shared an example of a headrest structure that travels between multiple sites — in California, Mexico and Oklahoma — before the final product is shipped from Chihuahua to the seat OEM.
“You can reduce all that in two parts, in two cities: one manufactures the metal and then in Chihuahua [at Soisa] we can do the whole thing and then send it to Gainesville. So, the less cities that we touch the better.”
Elsewhere, Soisa has for several years demonstrated its environmental, social and governance (ESG) credentials via a Waste to Wonder programme that sees it collaborate with an artisans’ cooperative from the local Tarahumara people who turn waste material into handmade handicrafts.
Working with the local government, Soisa also donates leather and fabrics to women in prison who create products and generate income for their families on the outside.
At the same time, however, the company has been actively exploring innovative ways to use sustainable materials such as those derived from pecan and corn shells or peel. And that work has already borne fruit.
In Hamburg, Soisa unveiled a new lightweight ‘organic armrest’ whose structure is made from a base of corn particles.
“We’re trying to substitute the foam made out of polyethylene to corn-based material. So we found this company in Switzerland that compresses the scrap of corn. It gets it into various presentations,” Mesta explained to RGN.
“This can be thrown into landfill and it will disintegrate,” said the Soisa executive, whereas polyethylene, “when you throw it into landfill, it stays there forever.”
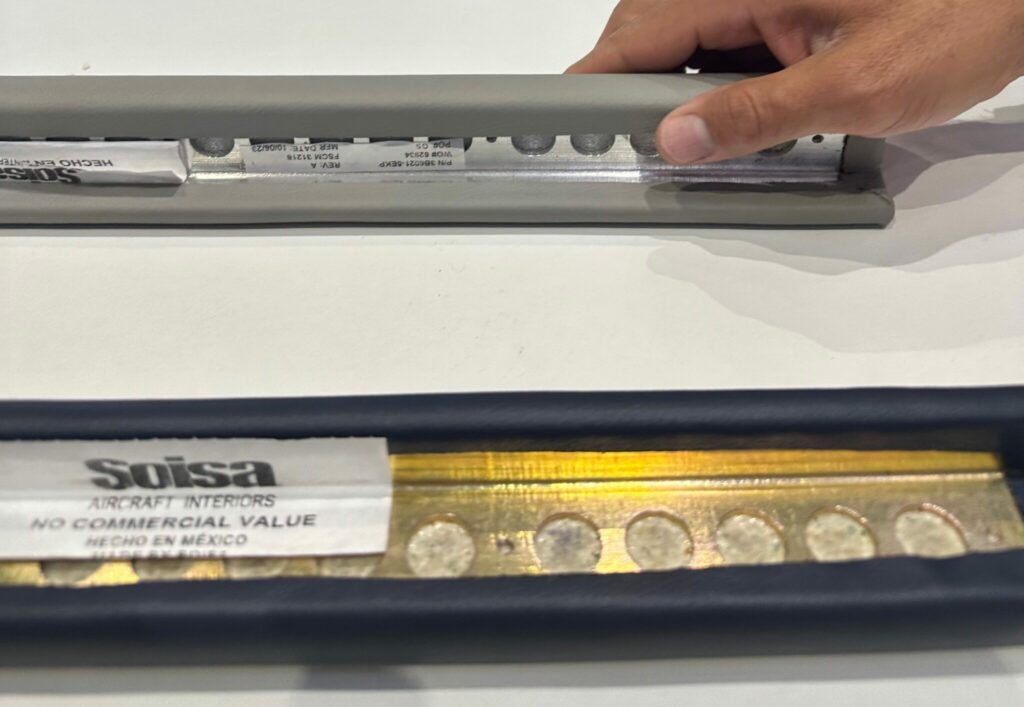
Soisa aims to certify the organic armrest, seen here in the foreground. An initial 12 second burn test went well. Image: Mary Kirby
Soisa counts a bevy of top-tier airlines as clients, including but not limited to United Airlines, Emirates, flydubai, Etihad, and Singapore Airlines. In 2023, it produced approximately 5,200 armrests, utilising around 2,000 square feet of polyethylene foam, which resulted in nearly 2,600 kg of CO2 emissions annually.
“By transitioning to a biodegradable material derived from corn waste, an eco-friendly, non-food resource, Soisa will significantly reduce its carbon footprint,” the company says in a statement. Notably, the aesthetics of the armrest don’t change, assured Mesta.
For Soisa, the organic armrest is just the start of what can be achieved. “We have other parts where we use a lot of foam; maybe not the bottom cushion, but there’s a lot of others that we can probably substitute this with,” he said.
Related Articles:
- Interior supply chain delays still hitting long-backlog Airbus
- Diehl Aviation pulls levers to tackle supply constraints: CEO Schuler
- Designing for sustainability: Soisa studies pecan shells for interiors
- Inside Airbus’ Airspace 2025 bin changes, including retrofits
- JAL A350 interiors supply chain issues raise spectre of delays in 2024
- Recaro Aircraft Seating CEO flags continued shortage in IFE parts
- With artisanal reuse partnership, Soisa focuses on ESG
Featured image credited to Mary Kirby