A new business class seat developed through a collaboration between Airbus, British Airways, Williams Advanced Engineering, JPA Design and SWS Certification, and sponsored by the UK’s Aerospace Technology Institute (ATI), aims to tackle the flight shame movement.
We’ve seen a push for lightweight interiors components for decades, as airlines operating on narrow margins had to contend with higher fuel costs. But public consciousness of airlines’ environmental impact has raised the stakes, and is moving the focus further forward on the plane.
This new business class seat concept would be 4kg lighter than comparable seating. The consortium calculates that by replacing all business class seats on 12 long-haul aircraft with their new design, airlines could save 942,000kg of CO2 and $195,600 in fuel every year, based on 40 business class seats per widebody aircraft.
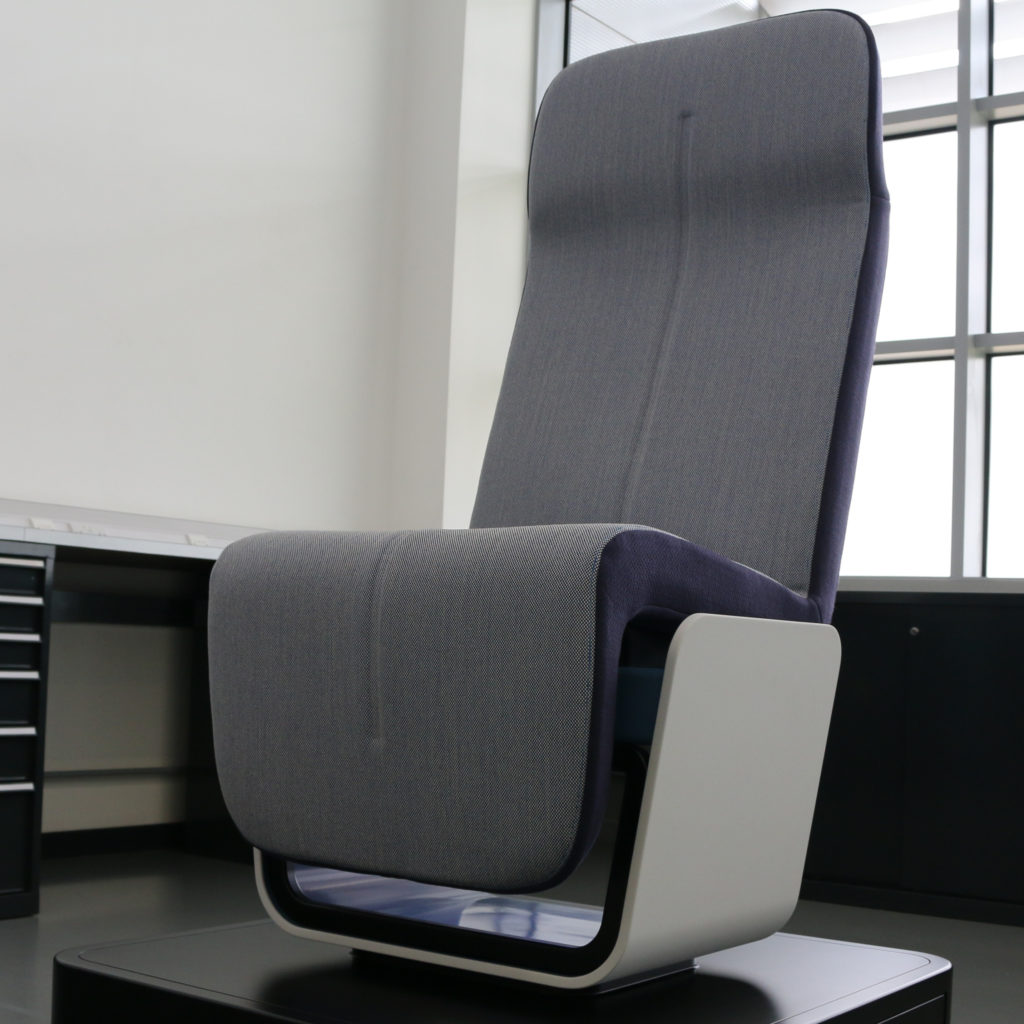
Variations of the seat design are intended to fit multiple aircraft, from the Airbus A320 to the A330 and A350, addressing premium seating demand for long-haul narrowbody aircraft too. Image: Williams Advanced Engineering
The weight savings on the new seat is the result of applied IP from the partners, including Williams’ ‘RACETRAK’ method for integrating unidirectional fibers and ‘223’ method for creating 3D structures from a 2D composite preform. This seat design will also require fewer parts in the bill of material, which will reduce both weight and costs.
Beyond helping airlines protect the planet, the new seat design could also improve aircraft safety. The designers have specifically looked at simplifying seat elements to reduce the risks of lithium-ion battery fires when PEDs will get jammed in seat mechanisms.
Williams has developed its engineering, testing and manufacturing competencies working in the competitive Formula One environment, where rapid innovation is prized. They have built up expertise in aerodynamics and advanced lightweight materials, among other competencies, which transfer well to aerospace manufacturing. The manufacturing process contributed by Williams Advanced Engineering can also be applied to other cabin structures to reduce the overall weight of the cabin.
The team at JPA Design has a well-established reputation for design of modern aircraft cabins. The firm has contributed its modular monocoque design to this project, and patented cabin layouts including an adaptable ‘tub’ for aircraft seating which optimizes the use of space for passengers and their luggage.
Airbus’ and British Airways’ contribution will be to help bring the product to market once it is developed. ATI’s support of the 18-month £1.4m ($1.7m) project is to strengthen aircraft interiors manufacturing competencies in the UK and create jobs.
The partners are also looking at a premium economy version, with that seat configuration contributing a 2kg weight savings.
“The UK has a strong existing industrial base for aircraft seat manufacture and an industrial strategy that highlights composites capability as a key area for development,” said James Park, founder and principal of JPA Design.
“This aligns to the ATI’s strategic outlook, creating products ready for the next-generation of aircraft. Our market-leading design and products such as the lightweight monocoque seating system, which allows for fewer parts, lower cost of manufacture, faster production time, lower maintenance and lower cost of ownership, as well as increased passenger space and comfort, will benefit significantly from the work of this consortium in turn providing enhanced opportunities for our airline customers.”
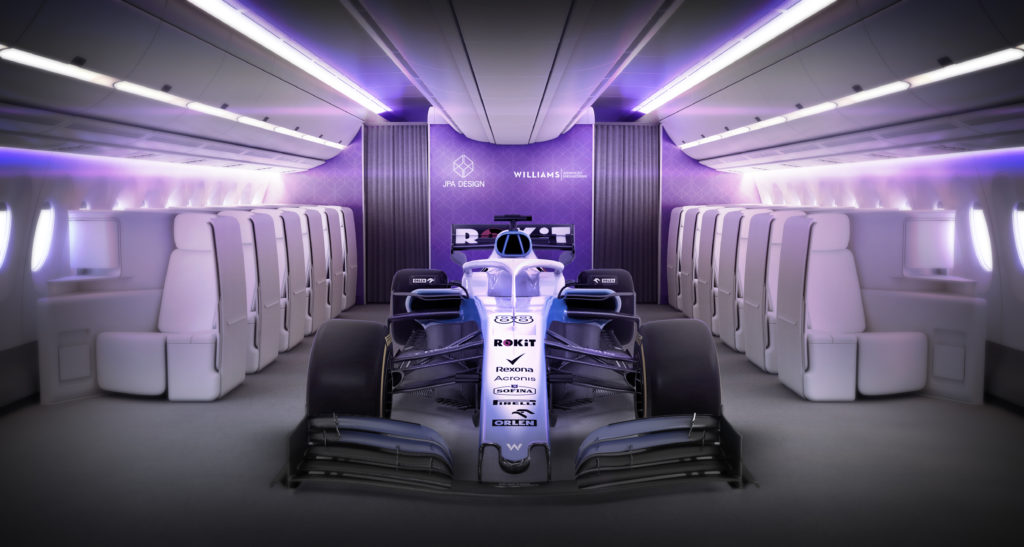
The key is modularity of components across airframes. Image: Williams Advanced Engineering and JPA Design
Related Articles:
- As Flight Shame movement gathers steam, IATA focuses on environment
- French aviation tax and internal flight ban highlight externality risk
- Key ways aviation is trying to improve its environmental credentials
- JPA’s Alex Duncan considers continuity of design in air travel
- PED battery fires on 777s prompt call for action
- Press Release: Williams Advanced Engineering and JPA team for #PaxEx
- PR Insight: The formula to deliver optimal aircraft seating